The process of plastic extrusion allows us to manufacture and materialise products that would otherwise have never seen the market. Here at Rocal Extrusions, we have been providing plastic extrusion services to a variety of industry sectors since 2009 and have gone from strength to strength in establishing ourselves as one of the main players in the extrusion industry. Whether it be for leisure home manufacturers, conservatory roofing or fenestration, we are able to provide plastic profiles for whatever your business requires. Today we wanted to go through how the plastic extrusion machine works so that you can be assured that you're fully aware of where your product is coming from. The process isn't as complicated as it may seem at first glance, and luckily, we're here to run you through it!
What is Plastic Extrusion?
To start off, what is plastic extrusion? Plastic extrusion is a high volume manufacturing process, otherwise known as plasticating extrusion. Through this process, raw plastic is melted and formed into a continuous profile. Once the process is complete, the finished product can be used for a variety of applications, including garden structures, office furniture or uses in the transport sector such as seating or trimming.
The Process Step-by-Step
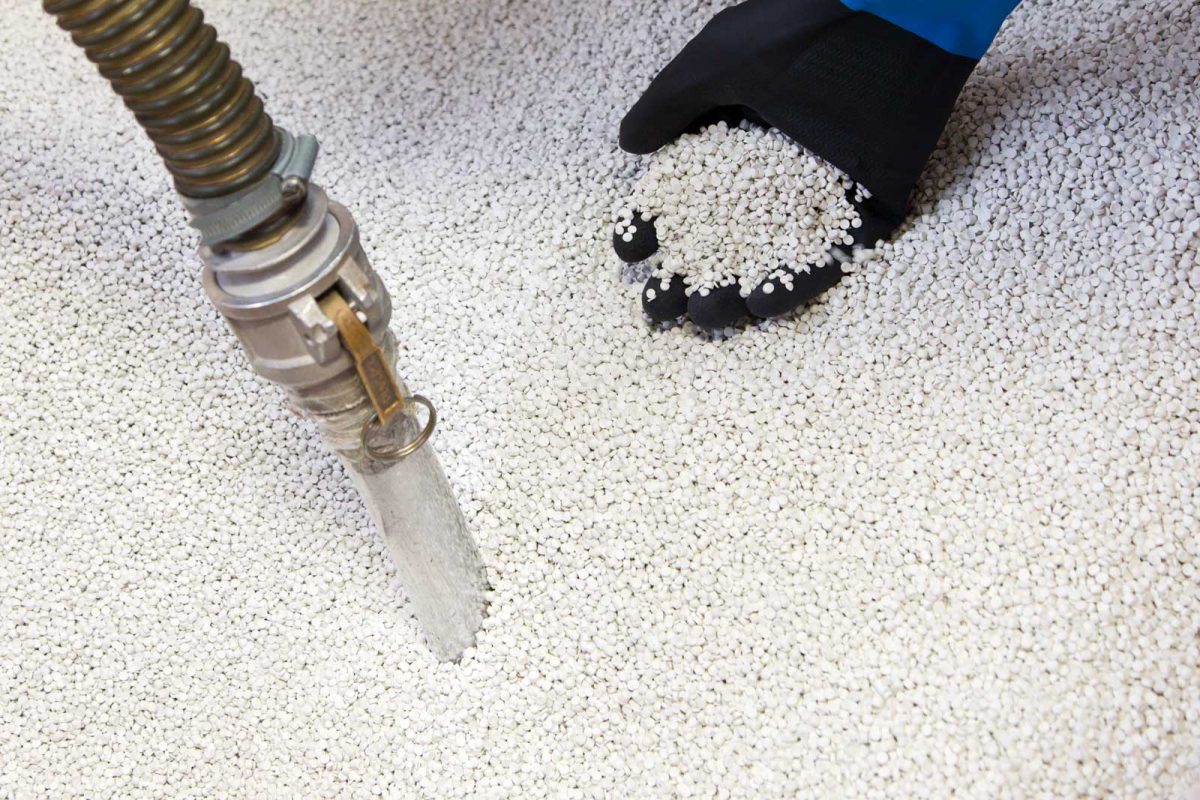
The process begins by taking raw compound materials. Usually, small beads, called resin, are fed into the top of the hopper. The hopper is the feeding tool that goes into the machine and works similarly to how a coffee grinder works. In the same way, as you put your coffee beans in the top of the grinder and they are fed down into the machine to be ground up, the hopper feeds the resin into the extruder's main chamber.
The main chamber is made up of two elements, a screw and a barrel. On the outside of the chamber is a motor which is driving the screw around the barrel. The barrel itself is heated, and the screw's rotation (usually at around 120rpm) pushes the resin beads through the barrel. As the beads pass through the heated barrel, they melt into a molten plastic. The barrel's temperature is heavily regulated to ensure that the beads melt slowly as they pass through the chamber so that there is no polymer degradation. Extra heat is provided by the intense pressure and friction between the screw, resin and barrel. If the chamber becomes hot enough, the heaters can be turned off, and the process can suffice on the temperature from the friction alone.
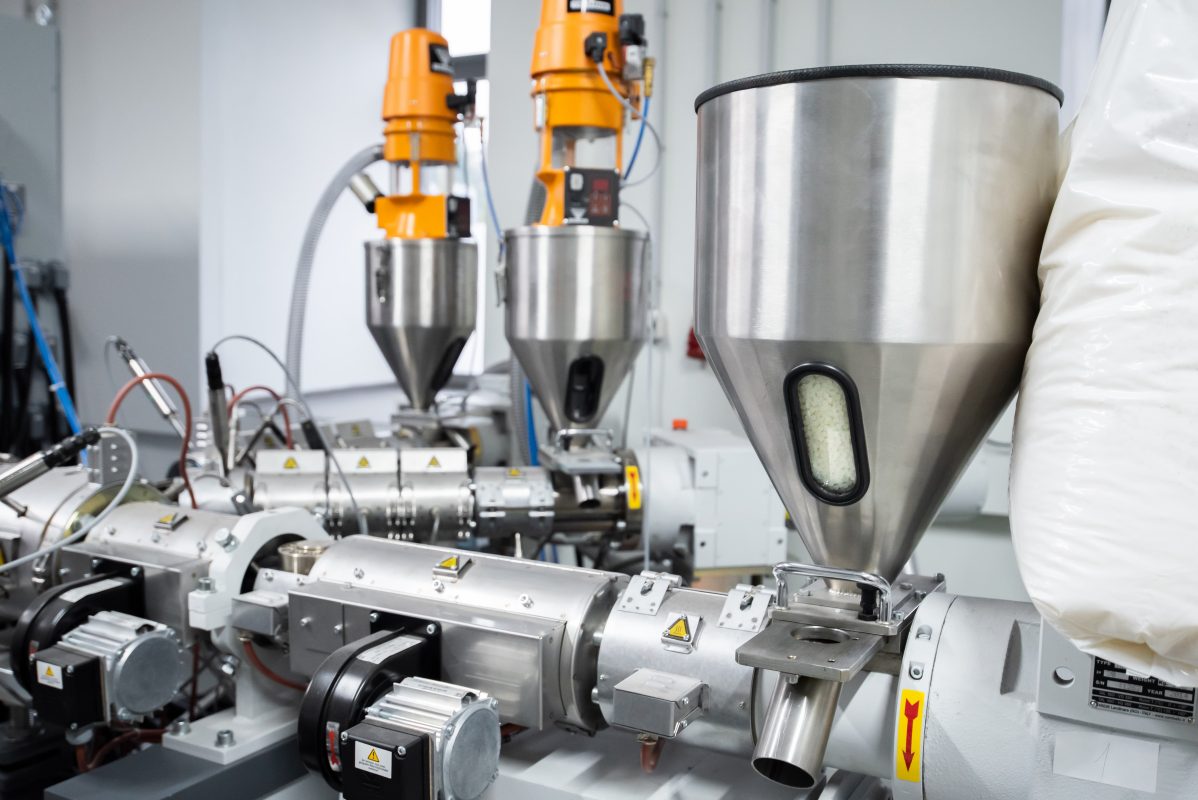
Once the molten plastic has passed through the entire barrel, it leaves the screw behind and passes into the breaker plate reinforced screen pack. The screen pack helps to remove any contaminants in the molten plastic. With the screen back and breaker plate, back pressure is created at the other end of the barrel. The backpressure is required to ensure uniform melting and the proper mixing of the polymer. How much pressure is going to be needed can be tweaked by adjusting the composition of the screen back, such as the number of screens, the weave size of the wires and various other parameters.
After passing through the screen pack to ensure there are no contaminants within the molten plastic, the hot material passes through the die. The die is what gives the product its profile and shape. The die is specially designed to allow even flow through this final part of the process to ensure consistency in the profiles. The shape of the die will determine what profile will be created at the end of the process, and therefore, this section is key for ensuring that the desired product is created.
As the molten plastic has passed through the die and has been shaped into its profile, the product needs to be cooled, usually bypassing the solution through a water bath. It isn't easy to cool plastic quickly because polymers tend to be very good thermal insulators, so they don't pass off the heat easily. The plastic passes through a tube which itself is submerged in cold water, and once passed the other side, the cooled plastic is now a hard profile.
Once the plastic comes out the other side, you have your plastic extruded product! Whilst it may seem complicated, the process is rather simple when broken down step by step. Here at Rocal Extrusions, we are experts in this process and are able to provide a whole range of profiles from extrusion. Whether you are looking for tubes, standard profiles, flexible profiles or rigid profiles, we can provide that for you. If you're interested in our services, please request a free quote for plastic tubes and much more through our online contact form, and someone will be back with you shortly!
We can't wait to hear from you.